October 3, 2018
U.S. ARMY CORPS OF ENGINEERS’
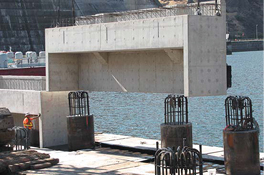
New Fish Transport Barge Moorage Wharf at Lower Granite Lock and Dam on the Snake River
Whitman County, Wash.
DESIGN & CONSTRUCTION TEAM
Project: USACE Lower Granite Dam Fish Barge Wharf
General Contractor: The joint venture team of Garco Construction, of Spokane, Wash. and Total Site Services, of Richland, Wash., (TSS/GARCO)
Owner: Walla Walla District United States Army Corps of Engineers
Precast Manufacturing Plant: Oldcastle Infrastructure – Spokane, Wash.,
Selkirk, New York and Edgewood, Maryland, Colorado
This U.S. Army Corp of Engineers’ project involves construction of a new moorage facility and mooring dolphin at Lower Granite Dam in Whitman County, Washington.
This new fish transport barge moorage wharf adds to the existing moorage facility located along the shoreline of the Lower Granite Dam earthen fill section to accommodate operations, maintenance, and repairs of the existing barge feet. The old wharf no longer had the maintenance capacity for the additional and larger barges being put into service the past few years, and crane access was limited. Lower Granite is the first salmon collector dam on the Snake River, and thus the primary component of the fish transportation program. The juvenile fish are barged around this dam and the others of the Snake and Columbia Rivers for release below Bonneville Dam to reduce their mortality.
The new barge mooring wharf is fabricated using a combination of cast-in-place and precast concrete. The 300 foot long by 40 foot wide moorage wharf rests on two rows of pilings — 32 steel drilled shafts, 54 inch in diameter and 41 feet in length.
Large cap beams sit side-by-side, over the pilings in the water. The bumpers on the outside face of the large pile caps protect the structure. The small cap beams also sit side-by-side, opposite the large ones, and run along the toe of the earthen fill section of dam. Pre-stressed slabs span between the cap beams. The on-shore and in-water pile caps and slabs are connected together by a final 6 inch thick cast-in-place concrete slab and closure pour tying the cap beams into the drilled shafts.
THE PRECAST CHALLENGE
“This project required precision precast manufacturing. The precast cap beams and slabs elements, which are very large pieces, had to be manufactured within exacting tolerances, within fractions of an inch, in order to site assemble the precast components and achieve the requirements of the wharf specifications”, said Chuck Prussack, P.E., for Oldcastle Infrastructure Spokane. “We created a 3D virtual mock up based on as-built information to ensure that when the large precast concrete pieces arrived at the site they would fit with precision. In addition, there were special transportation requirements. The large cap beams required a truck and trailer measuring 138 feet long, and the road into the construction area was a narrow, winding two-lane country road with switch backs and a steep grade to the river.”
Oldcastle Infrastructure manufactured and shipped the eight-36 foot long by 7 foot wide by 13 foot high precast concrete large cap beams (140,000 pounds apiece), eight-36 foot long by 7 foot wide by 9 foot high small cap beams (104,000 pounds apiece), and thirtytwo- 27 foot long by 9 foot wide by 1 foot-6 inch thick pre-stressed concrete slabs (56,000 pounds apiece), for the barge moorage wharf project.
OLDCASTLE INFRASTRUCTURE PRODUCT USED
- (8) 36 foot long by 7 foot wide by 13 foot high precast concrete large cap beams (140,000 pounds apiece)
- (8) 36 foot long by 7 foot wide by 9 foot high small cap beams (104,000 pounds apiece)
- (32) 27 foot long by 9 foot wide by 1 foot-6 inch thick pre-stressed concrete slabs (56,000 pounds apiece)
USE OF PRODUCTS
Construct a new dam moorage wharf
WHY SELECTED
Precast concrete products reduced environmental impact, provided rapid construction, improved constructability, increased quality, and lowered life-cycle costs. Constructing the over water wharf in this manner provided the most efficient and durable solution for the USACE.
DATE OF INSTALLATION
Last Pieces October, 2014
INNOVATION
Providing a high quality, durable precast concrete approach to an interesting construction challenge — limitations of working in the river, tight construction schedule, and production within exacting tolerances of large precast components for field assembly– shows an excellent use of how precast concrete construction can accelerate a construction schedule and easily overcome demanding challenges of a project that other methods could not have achieved. The $6.9 million U.S. Army Corps of Engineers state- of-the-art precast/prestressed concrete wharf system reduced environmental impact, provided rapid construction, improved constructability, increased quality, and lowered life-cycle costs. Constructing the over water wharf in this manner provided the most efficient and durable solution for the USACE in addition to allowing service cranes to access any barge that is moored there.