February 6, 2025
Revolutionizing Underground Enclosures
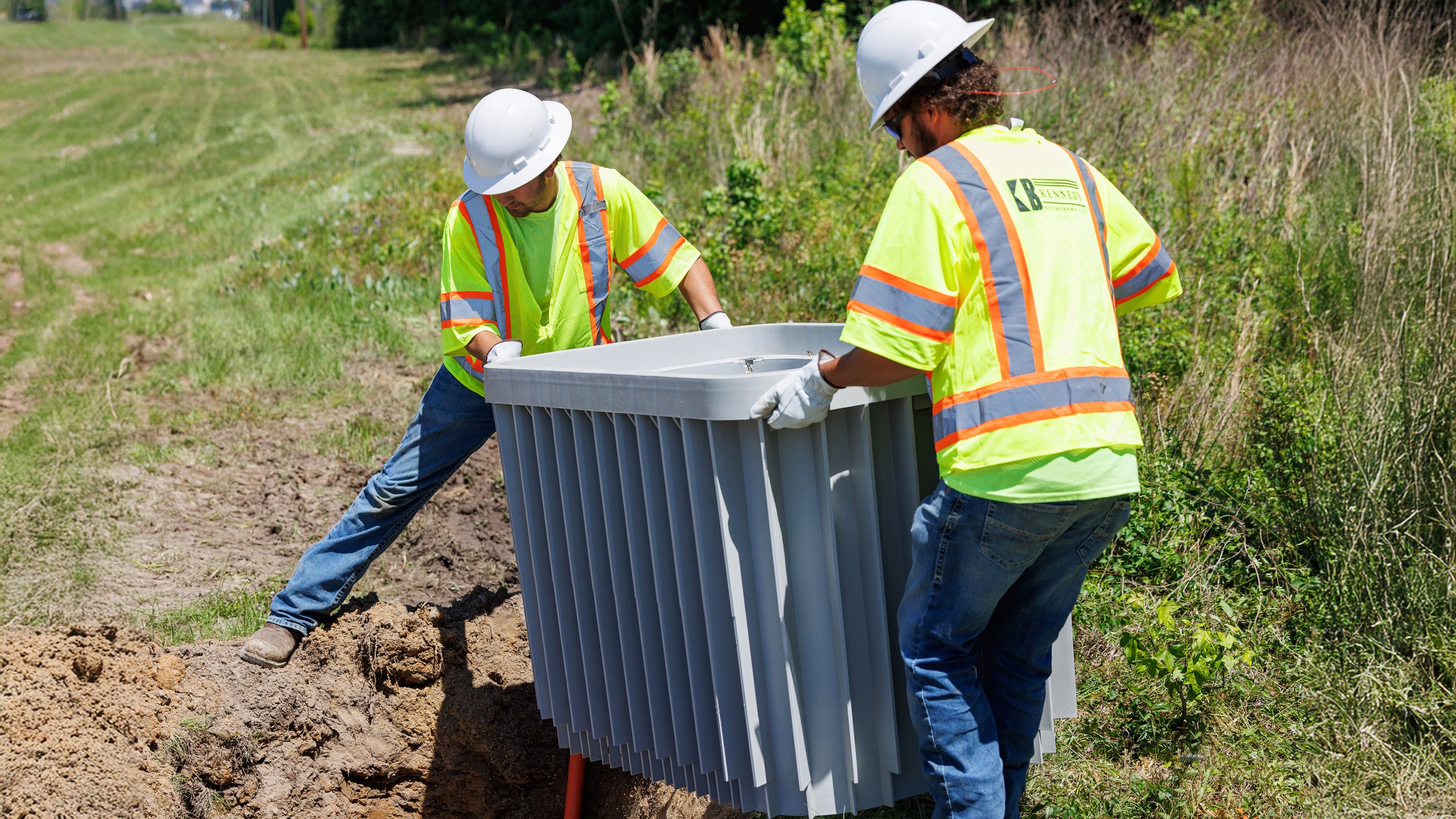
Underground enclosures are crucial to provide access to fiber networks and electrical equipment while protecting them from frost, rust, and the elements. For decades, these enclosures have been constructed from polymer concrete – a heavy and bulky composite product.
There had to be a better solution, and Oldcastle Infrastructure’s product team came up with the answer: Duralite®.
The lightweight enclosure solution
With safety, efficiency, cost savings, and eco-friendliness at its core, Duralite is a lightweight alternative to polymer concrete handholes. Designed to exceed product performance standards for polymer concrete, Duralite is also 50% lighter than the old technology.
This weight reduction creates value for buyers and end users downstream by reducing overall installation time, maximizing equipment efficiency, and mitigating safety risks. Duralite also meets all ANSI SCTE 77 performance standards.
Built to take the heat
Duralite is engineered to withstand high temperatures from heatwaves and wildfires. The product exceeds the standards in the ANSI/SCTE 77 section 6.5, ASTM D635 as well as and US Dept of Agriculture, Rural Utilities Service, 7 CFR 1755.910 – (e), 3 xiii, requirement A.
This enclosure is designed to keep utility and service provider assets safe and functional even in a high-temperature environment.
Lower environmental impact
Oldcastle Infrastructure is committed to improving manufacturing methods to be more sustainable. Duralite enclosures contain up to 65% recycled materials. Its eco-friendly profile allows easier and lighter transportation options, which translates to saving money and carbon footprint.
Compared to polymer concrete, Duralite is a no-brainer for saving time, money, and the environment.
Saves time, reduces cost
Duralite is easier to maneuver at the inventory yard and installation site. Its reduced weight allows contractors to use lighter duty equipment like pickup trucks instead of flatbeds. This translates into fuel cost savings and a lower carbon footprint.
The revolutionary product also maximizes excavator efficiency. With Duralite, an excavator can dig one hole and immediately move on to the next installation site. This is because most Duralite products can be safely lifted and installed by two people by hand while the excavator is prepping the next installation site. This reduces installation time and the need for heavy-duty equipment while helping contractors install more boxes faster.
Data from multiple installations reveals that contractors complete their projects 30% faster by using Duralite instead of traditional polymer concrete.
Safer design limits injuries
Since Duralite is 50% lighter and easier to lift than polymer concrete, it reduces the risk of injury associated with maneuvering and leveling the box during installation. If a Duralite box falls on someone, they can walk away from the injury; the same incident with polymer concrete could result in severe injury or loss of life.
Dropping the cover into the body of a handhole is
risky for hand and finger injuries as well. Since Duralite covers are significantly lighter than polymer concrete, installers are much less likely to break their fingers when inserting the cover into the box.
Lighter and better in every way
When choosing the right Tier 15 or Tier 22 enclosure to complete your job, the overall improvement of Duralite compared to polymer concrete cannot be understated. Duralite is lighter, faster, safer, easier to modify in the field, and results in a lower carbon footprint – helping communication service providers and utilities save time, money, and the environment.
Broadband contractors can see the difference
On a recent project we shadowed a customer, Kennedy Broadband, along Hwy 17 in Richmond Hill, Georgia to compare the installation of polymer concrete versus Duralite.
The team at Kennedy Broadband related how they have switched to Duralite because of the lightweight solution, which positively impacted crew safety and cost savings for fuel and equipment.
James Kennedy, operations manager at Kennedy Broadband said it best:
“Sometimes we’re asked what we would prefer to use by our customers, and I would definitely prefer a Duralite versus polymer concrete because we’re minimizing the injury potential, the need for heavier axle trailers and heavier trucks to move vaults. Oldcastle has the technology to build a lighter, yet strong, tier-rated box and I would say don’t think about the old days – go with Duralite.”