October 3, 2018
SEATTLE’S NEW ELLIOTT BAY SEAWALL
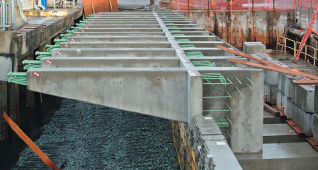
Precast Concrete “Z” Superstructures and Wall Panels Used to Construct
Seattle Washington Waterfront, Seattle, WA
DESIGN & CONSTRUCTION TEAM
General Contractor: J E Dunn Construction
Project Manager: Kyle Quigley
Owner: City of Seattle, Wash.
General Contractor: Joint Venture team of Mortenson-Manson, general contractor/construction manager (GC/CM).
The Elliott Bay Seawall project, part of Seattle’s Water-front Program, is a joint effort between the City of Seattle Department of Transportation {SDOT), and the U.S. Army Corps of Engineers {USACE) to replace the 100 year old seawall. Built between 1916 and 1936, the failing wall has suffered significant timber decay and deterioration of the structure from continued exposure to storm waves and tides, including damage from the magnitude 6.8 Nisqually Earthquake. Oldcastle Infrastructure, Auburn, WA was selected by the Joint Venture team of Mortenson-Manson, general contractor/ construction manager {GC/CM), to supply precast concrete Z-shaped superstructure segments and 20-foot tall seawall face panels for the reconstruction of the new $330 million Elliott Bay Seawall at the waterfront in downtown Seattle, Wash.
THE CHALLENGE
Acting as a barrier between Elliott Bay and the waterfront, the new seawall structure consists of a cast-in-place support slab with custom precast concrete face panels, precast concrete zee shaped superstructure segments, and precast sidewalk panels. The precast elements were designed to be connected to the support slab by closure walls and a shear block. Once the “Z” superstructure segments were in place, concrete was poured to form a closure wall and edge beam, which connects the zee panels to each other on the land side and the waterside, respectively. This innovative solution resulted in expedited construction and minimized the impact on adjacent piers, which are valuable sources of tourism for the city.
To successfully construct the new seawall, Oldcastle Infrastructure worked closely with Mortenson-Manson and Paron’s to complete the design and engineering of the fascia panels and specialty “Z” superstructure segments essential to the seawall’s stability. The “Z” superstructures were a critical step in building the seawall and acts as the concrete backbone of the new seawall’s cantilevered sidewalk. These large, zee-shaped concrete segments provide a counter-balance and support structure for the new overhanging sidewalk.
In all, 400 precast concrete “Z” superstructure segments, 8-foot wide by 9-foot tall, that extend 13-feet and 400 precast concrete fascia panels, with various architectural finishes, measuring 8-ft-wide by 20-ft-tall with a thickness of 15 inches were manufactured and shipped by Oldcastle Infrastructure.
OLDCASTLE INFRASTRUCTURE PRODUCTS USED
- (400) “Z” Superstructure Segments: 8-foot wide by 9-foot tall, and extend 13-feet over the waterfront.
- (400) Fascia Wall Panels, with various architectural finishes, measuring 8-foot wide by 20-foot tall with a thickness of 15 inches. There are three different wall face designs throughout the project area, including tide lines, cobblestone and marine life textures.
USE OF PRODUCTS
Construction of a Seawall
WHY SELECTED
Precast concrete products reduced environmental impact, provided rapid construction, improved constructability, increased quality, and lowered life-cycle costs. Constructing Elliott Bay’s Sea Wall in this manner provided the most efficient and durable solution for the City of Seattle.
INNOVATION
Seawalls protect homes and businesses by withstanding some of the most violent conditions any marine product must endure.
The design and engineering of the fascia panels and specialty “Z” superstructure segments were essential to the seawall’s stability. The “Z” superstructures were a critical step in building the seawall and act as the concrete backbone of the new seawall’s cantilevered sidewalk and provide a counterbalance and support structure for the new overhanging sidewalk.
Providing a high quality, durable precast concrete approach to an interesting construction challenge – limitations of working in constrained area, tight construction schedule, and production within exacting tolerances of large precast components for field assembly – shows an excellent use of how precast concrete construction can accelerate a construction schedule and easily overcome demanding challenges of a project that other methods could not have achieved.
The state-of-the-art precast concrete seawall system reduced environmental impact, minimized the impact on adjacent piers, provided rapid construction, improved constructability, increased quality, and lowered life-cycle costs.
Find out more about Oldcastle Infrastructure Precast Concrete Seawall Systems.