As digital technology becomes increasingly essential to daily life, the demand for high-speed broadband in residential neighborhoods is skyrocketing. From telecommuting and online learning to smart homes and streaming, reliable internet access is the backbone of modern living. To meet these growing demands, efficient fiber-to-the-home (FTTH) deployments are more critical than ever.
But broadband infrastructure is more than just connectivity—it’s a foundation for thriving, connected communities. The challenge lies in creating scalable, sustainable networks that can evolve with emerging technologies and user needs.
At the heart of this effort is the need to streamline the installation process to ensure reliability, reduce costs, and accelerate deployment. Our comprehensive suite of products and industry expertise empowers professionals to build FTTH networks that are not only faster to install but also built to last.
Essential Tools for High-Quality Broadband Installation
Successful broadband deployments require more than just cables—they demand precision, efficiency, and the right tools. Here’s what professionals need to ensure clean, reliable installations:
- Structured Wiring Systems: Media panels and network modules/switches serve as central hubs, organizing complex smart home networks and simplifying ongoing maintenance.
- Tool-less Components: Distribution modules and jacks designed for quick, tool-free connections save valuable time during installation without sacrificing quality.
- Distribution Modules: Voice and data modules with front punch-down access expand functionality in single-family units (SFUs) and multi-dwelling units (MDUs), all within compact media enclosures.
- Crimping & Cutting Tools: Keystone jack crimping tools ensure accurate terminations for Cat5e and Cat6 cables. RJ crimping tools are essential for Cat6 and Cat6a snap plug projects. Flush cutters provide precise trimming in tight spaces, keeping installations clean and efficient.
Support from the Ground Up
Oldcastle Infrastructure offers proven solutions to support broadband expansion—from fiber routing components and media panels to weather-resistant enclosures. Whether you’re rolling out FTTH to a single home or scaling across entire communities, we help you build faster, smarter, and with greater confidence.
Explore our full line of communications solutions and see how we can help you meet today’s broadband challenges head-on.
As the demand for high-speed internet continues to grow, broadband providers and installers face increasing pressure to accelerate fiber-to-the-home (FTTH) deployments—particularly in neighborhoods not originally designed for fiber infrastructure.
Across the U.S., brownfield retrofit projects are gaining momentum, driven in part by initiatives like the Broadband Equity, Access, and Deployment (BEAD) program. These upgrades are critical to bridging the digital divide, but they also bring a host of logistical challenges—from scheduling technician visits to securing home access and completing installations with minimal disruption.
To overcome these hurdles, service providers are turning to smarter, more efficient methods that streamline in-home installation and reduce time spent in the field.
Preloaded Panels: Reducing Time On-Site
Traditional FTTH retrofits often require technicians to perform every step on location—setting up panels, terminating cables, and installing components—which increases labor costs and complicates scheduling, especially in multi-unit buildings or homes with limited access.
A more efficient approach is the use of preloaded media panels. These panels are fully wired and outfitted off-site with essential components like network equipment, adapters, and cable routing. Once on-site, installers simply mount the panel, connect fiber and power, and activate service—significantly reducing installation time and homeowner disruption.
This approach offers several key benefits:
- Shorter installation windows
- Lower labor costs
- Greater consistency and quality
- Faster broadband rollouts across multiple homes
Designed for Brownfield: Retrofit-Ready Media Panels
Choosing the right panel for retrofit environments is essential. The SOHO Pro media panel, part of our Primex product line, is purpose-built for in-premise retrofits. It’s engineered to support structured wiring in existing homes and is flexible enough for both wall-mounted and freestanding installations.
Its slim profile integrates easily into residential settings, while built-in knockouts allow for simple routing of fiber and power. When preloaded in advance, the panel further enables:
- Clean, professional cable management
- Fewer installation errors
- Faster, tool-free setup on-site
In time-sensitive and access-restricted retrofit scenarios, solutions like the SOHO Pro PR10, PR1500 or PR2300 help teams stay efficient and on schedule—without sacrificing quality.
Scaling FTTH with Confidence
The demand for broadband retrofits shows no signs of slowing. With nearly one-third of U.S. homes still lacking reliable internet access, service providers need scalable, efficient strategies to meet rising expectations.
Preloaded panel solutions deliver exactly that. By shifting complex prep work off-site, they minimize on-site errors, enhance consistency, and enable installers to move quickly from one home to the next.
At Oldcastle Infrastructure, we support the future of broadband with field-proven solutions—from enclosures and media panels to fiber management accessories. Whether you’re upgrading a single residence or deploying fiber across entire communities, we help you move faster, meet demand, and build with confidence. Discover our full range of communications solutions.
Aging water infrastructure is an issue in the United States. Texas is working hard to address it, but it will benefit from also working smarter.
Aging infrastructure is a significant challenge, with parts of the US still relying on water utility pipelines that were laid down before the turn of the century. The turn of the 20th century, that is.
This issue is typically thought of as being more prevalent east of the Mississippi, in our older towns and cities, but it would be a mistake to think that the west of the country is not similarly at risk. While it’s true that the average age of pipelines is lower, they are nonetheless reaching or exceeding their design lifetime; Texas is a case in point.
Non-revenue water in Texas
Texas has over 165,000 miles of pipeline spread across more than 7,000 systems in its water supply network, with the average year of installation for those pipes being 1966.
Aging infrastructure is more prone to leaks, causing what’s known as non-revenue water, or NRW—water that is abstracted, treated and supplied, but lost before reaching consumers—and as a result, the largest cities in Texas are losing around 88 billion gallons of water per year:
- Houston: 31.8 bn
- San Antonio: 19.5 bn
- Dallas: 17.6 bn
- Austin: 7.1 bn
- Fort Worth: 5.9 bn
- El Paso: 4.8 bn
Houston and Dallas also saw large increases in water loss over previous years—30% and 18% respectively—indicating that the issue is worsening. Indeed, in its 2025 Texas Infrastructure Report Card the American Society of Civil Engineers gave the state a D+ grade overall for its drinking water, down from C- in 2021.
In a state beset by growing demand coupled with water scarcity and climate-related issues, residents have identified the need to make changes, and in 2023 passed a proposition to create a fund to pay for infrastructure projects.
Providing $1bn of funding to invest in water loss and water quality issues around the state, this represents a positive step, but it is estimated that Texas will need to invest over 150 times that amount over the next 50 years in order to adequately address all of its water infrastructure issues.
Addressing water loss
So how can utilities in Texas tackle this challenge?
The answer is in effectively prioritizing repairs. Knowing that there are leaks is one thing, but knowing where those leaks are is another thing entirely. Water utilities typically budget to replace ~1% of their water distribution network every year, and generally replace the oldest sections of the network first, but this isn’t always the best course of action.
While it’s true that the risk of leakage does increase with the age of the pipe, other factors also come into play: geological movements, corrosion due to high or low soil pH levels, and accidental damage all factor into the condition of pipes.
The fact is that there are older pipes that retain their integrity, and there are newer pipes that leak. As Indiana Jones once said: it’s not the years, it’s the mileage.
Leak detection techniques
So what can water utilities do?
On paper it’s very simple: identify the location of the leaks, assess the volume of water being lost through those leaks, and prioritize upgrading the areas with the biggest losses first. However, water pipes are buried underground, and leaks are unlikely to be conveniently located in a manhole.
Traditionally, utilities have relied on somewhat simplistic leak detection techniques such as sniffer dogs or listening sticks. These suffer from inconsistency and limited reliability, with detection success rates sometimes estimated in the 30-40% range. New technologies such as CivilSense™, however, take this approach and bring it into the 21st century.
CivilSense uses a range of data sources to analyze a water supply network, using artificial intelligence to identify areas of high water loss. Advanced acoustic sensors are then placed strategically at points in the sections of the network experiencing elevated water loss, and the AI then analyzes the acoustic data to pinpoint the location of each leak and assess its size.
Armed with this information, utilities are able to prioritize or redirect scheduled network replacement activities and undertake any necessary emergency replacement work, ensuring that their resources are targeted specifically to the areas of the network that are experiencing the largest losses.
Conclusion
As we’ve seen, Texas faces significant challenges in overhauling and upgrading its aging water infrastructure, but the state is responding in positive ways. Increased investment and increased public enthusiasm are elevating the issue and driving change, which is to be applauded.
However, the challenge is large and complex, and 20th century approaches won’t fix 21st century problems. Texas is working harder—but it will benefit from also working smarter.
Next
Internet needs at home are changing fast. Between remote work, smart home gadgets, and streaming in 4K (or higher), today’s households are using more bandwidth than ever. In fact, from 2020 to 2023, average household internet use jumped more than 30%. And it’s not slowing down.
The typical U.S. home now has over 21 connected devices—up from just 11 a few years ago. That’s everything from laptops and tablets to smart thermostats, security cameras, and gaming consoles. With all this demand, networks need to do more—and do it better.
To keep up, builders, broadband providers, and planners are turning to Category 6A (Cat6A) cabling. It is not just about futureproofing anymore—it is about meeting today’s performance expectations.
Why Cat6A Cabling Makes Sense Now
Cat6A cabling can handle 10 Gigabit Ethernet speeds over longer distances and supports twice the bandwidth of Cat6. That means fewer slowdowns and smoother performance—even when the whole household is online at once.
It’s also great for powering connected devices. Thanks to support for newer Power over Ethernet (PoE++) standards (up to 90 watts), Cat6A can deliver both power and data to smart devices like cameras, lighting systems, and sensors—no extra wiring required.
In most new builds, Cat6A works alongside fiber that brings high-speed internet to the building. Inside the home, it helps spread that speed to every room.
It’s Not Just the Cable—Hardware Matters Too
To get the most from Cat6A cabling, it is important to use the right setup. It also requires smart installation practices and well-matched connectivity hardware.
Products like Oldcastle Infrastructure’s Primex PR10 Media Panel provide a centralized hub for network devices, while the FTC2 Fiber Wall Plate and P350 enclosures help organize and protect connections from the outside drop to the in-unit endpoint.
These tools make structured cabling easier to install and maintain, especially in homes with tight spaces or retrofit conditions.
Cat6A Cabling: a Must-Have for Multi-Unit and Mixed-Use Projects
In apartment buildings and mixed-use developments, structured cabling is no longer a nice-to-have—it is essential. Developers are looking for systems that:
- Support more devices
- Offer faster speeds and lower latency
- Make upgrades and maintenance easier over time
Industry groups like TIA and BICSI continue to recommend structured cabling for exactly these reasons. And federal programs like BEAD (Broadband Equity, Access, and Deployment) are backing projects that bring reliable, high-speed internet to more communities.
While BEAD doesn’t call out Cat6A by name, its goals—long-term reliability, scalability, and equity—line up perfectly with what Cat6A delivers.
Overcoming Barriers to Cat6A Adoption
Cat6A cabling used to have a reputation for being more expensive and trickier to install, but that’s changing fast.
- Installers are getting trained and more comfortable with it
- Costs have come down as more projects adopt it
- Growing bandwidth demands make it harder for older cabling standards to keep up
For anyone planning networks that will last well into the future, Cat6A is a smart, affordable choice.
Ready for What’s Next
When you combine Cat6A cabling with the right gear, you get faster, more reliable networks—whether you are wiring up a single home or a whole community.
At Oldcastle Infrastructure, we are here to help with a full line of proven solutions to make FTTx and structured cabling installs smoother, faster, and more dependable. Learn more about our communications solutions.
Efficiency through improved grit removal
The demands on wastewater treatment are greater than ever before, putting upgrades and refurbishment firmly in the spotlight, but with a firm requirement to manage costs.
Wastewater treatment works upgrades are an essential part of ensuring the modern plant continues to meet its discharge consents in the face of tighter standards, population growth and increasing water use.
Achieving these aims while facing reduced budgets and the demand to maximize ROI is a major challenge.
How can plants be upgraded without incurring additional costs?
One obvious way that plants can be upgraded is often overlooked: grit removal.
Sitting at the head of the treatment train and furthest from the regulated point of discharge, grit removal is often seen as a minor part of the treatment process. This can be detrimental to a project as it’s an essential element that can significantly help with the challenge of cutting operation and maintenance costs.
Grit removal improvements remain a less-favored option. While the costs of removing grit and maintaining a detritor are well known, the OPEX (operational expenditure) cost of not removing grit effectively is less clear.
Detritors do not cause compliance issues, and the cost of removing grit is often transferred to other sites within the plant. This particularly happens where sludge is digested, meaning that funding is deflected or deferred beyond the utility’s usual short financing cycle.
One of the key issues is that grit removal is normally restricted to particles larger in size than 200 μm (microns) (see Wastewater Engineering: Treatment and Reuse by Metcalf & Eddy). However, typically around 40% of inorganic influent material is smaller than this.
The cost of inefficiencies
Without an effective and efficient grit removal and capture system, various costs rise significantly: not only is power usage substantially increased, the maintenance commitment to all downstream processes is also negatively impacted.
This is partly due to the abrasive nature of grit. Grit increases the amount of wear and tear that moving parts, such as pump impellers, are subjected to.
If grit is not captured in the detritor, it will settle out in other parts of the treatment train. The consequences of grit settling out in unwanted areas include blockages in pipes and channels, and reduced capacity in the downstream treatment tanks.
Lack of capacity impacts on the flows that can be treated (or in a digester, on the hydraulic retention time) and, as a result, upon the effectiveness of the treatment and the quality of the final discharge. It also means that expensive and time-consuming manual removal is required. This leads to increased downtime for vital processes and the need to consider health and safety implications.
The value of high-performance grit removal
Improving the amount of grit collected at the head of the works is an attractive option that can ensure downstream processes function correctly and remove or postpone the need for upgrading (and consequently, the costs of the improvements).
The correct application of a high-performance grit system reduces lifetime energy costs and can help reduce the whole life costs of capital equipment. This is done by extending the time between maintenance periods, reducing blower usage in aerated systems, and cutting the amount of downtime required for grit removal.
Takeaways
- Cutting the cost of an upgrade depends on ensuring that processes such as grit removal are working to optimum capacity.
- By improving the amount of grit collected at the head of the works, general wear and tear can be avoided—eliminating high maintenance costs.
- Without an effective and efficient grit removal and capture system, various costs rise significantly.
Wastewater treatment plant upgrades are an essential and ongoing part of the treatment process. Here’s what you need to consider when upgrading your site.
Utilities face various key considerations when it comes to upgrading wastewater treatment plants (WWTPs). This includes any improvements required by legislation, such as the discharge limits and conditions for discharges mandated by the EPA.
The EPA is also conducting a nationwide nutrient removal study that could have major implications for the country’s widespread nutrient pollution.
Make performance a priority
All utilities are measured against their performance in meeting their various targets, and compliance is increasingly important as regulation becomes more stringent.
The issues that consultants and contractors face when upgrading WWTPs start with a lack of funding, which is an ongoing issue driven by regulatory caps on profits and/or reduced municipal investment.
Utilities need to fully justify the costs of any changes, maintenance costs need to be kept to a minimum, and the rising cost of energy needs to be managed.
The aim is to boost ROI and reduce capital expenditure (CAPEX), while ensuring the treatment works still meets its consents and any key performance indicators (KPIs).
Increase capacity and space
There is also a need for increased capacity. The urban population is soaring – over 50% of the world’s people live in urban areas, and more towns and cities are developing.
If a WWTP is struggling due to a lack of capacity, the risks of causing water pollution increase sharply. Managing stricter discharge limits and increased effluent discharges adds to the pressure on utility consultants and contractors to meet consents without driving up costs.
Space is another key consideration. As urban areas encroach upon wastewater treatment works that were once outside the urban perimeter, they restrict the land available for expansion.
It is essential that contractors offer options that have a small footprint or can be installed within existing treatment space. It is always necessary to look at space-saving options first, and determine the element of rebuilding that is involved.
Choose a good grit removal system
It is important that grit removal upgrades are considered at an early stage, as ineffective grit removal is one of the main causes of downstream problems in wastewater treatment works.
Consequences include:
- A lack of capacity in treatment tanks
- Increased energy costs
- Reductions in the effectiveness of treatment
- Breaches of consents
Choosing a good grit removal system in itself involves various considerations, not least the size and character of grit that needs to be removed.
In design, it is important to recognize that wastewater grit is not homogenous – it consists of a wide variety of materials, often much smaller and more irregular than the 212 µm (micron) diameter perfect dry sphere that is typically assumed.
Grit can consist of particles washed from roadways and other urban surfaces, and can comprise sand, paving materials, eggshells, coffee grounds, seeds, fragments of bone and many other constituents, any of which can also become attached to fat, oils and grease (FOG), making it difficult to settle.
Conclusion
Getting grit removal right not only has significant benefits to downstream assets, but it also saves a great deal of money.
Research from Cranfield University in the UK has estimated that for a 6.5 mgd plant with an asset life of 25 years, the total cost of extraneous grit would be around $0.93 million, and the calculated break-even capital cost of advanced de-gritting based on mitigating 50% of the remediation costs is $0.56 million.
Therefore, when starting the upgrade process, grit removal has to be one of the major considerations.
Takeaways
When upgrading a WWTP, owners, engineers and contractors should consider:
- Changes to legislation that may impact upon the requirements for discharges.
- Population increases in the treatment works’ catchment area that may mean flows to the works have increased substantially.
- The funding available for any upgrades that are needed.
- The space available for the proposed upgrades.
- The impact that improved grit removal will have on all downstream processes, including maintenance, capacity, treatment efficiency, and wear and tear.
The appetite for fiber Internet service is surging. As of 2024, 76.5 million homes across the United States are now connected with fiber to the Internet, marking a significant year-over-year increase. Such rapid expansion means a wide array of professionals, including builders, installers, engineers, architects, and service providers, are increasingly engaged in introducing fiber service to new residential developments and retrofitting existing structures. This task demands careful planning and a deep understanding of fiber architectures and their specific components.
As global demand for reliable broadband spikes, Oldcastle Infrastructure continues to lead with innovations that improve fiber-to-the-x (FTTx) deployments. Our broadband and connectivity solutions are crucial for developing efficient, scalable, resilient broadband infrastructure for modern digital landscapes and smart city projects.
The national push for widespread fiber deployment is not just about faster internet speeds; it’s about economic revitalization, healthcare access, educational opportunities, and bridging the digital divide. In areas still lacking adequate connectivity, Oldcastle’s strategic deployment practices are more than infrastructural developments; they are community lifelines.
An example is the Fort Collins project, which highlights how our integrated solutions extended broadband across multiple communities. For this project, the planners adopted a neighborhood-wide approach to fiber-to-the-home (FTTH) deployment instead of focusing on individual homes, as a highly efficient way to create the infrastructure. The incremental effort and cost required for an ISP or a technician to install fiber connections for multiple homes versus just one are relatively small. Yet, the rewards – such as heightened uptake of fiber packages once the infrastructure is established – are significant.
But navigating a neighborhood-wide FTTH deployment demands more than just a top-notch team. It also requires the proper installation to drive efficiency, minimize costs, and ensure the job gets done right the first time. The project required detailed planning and staged installations, with many Oldcastle products to comply with high-quality standards.
Integrating fiber optic technology is fundamental in evolving urban development. With the inclusion of our Primex product line, Oldcastle Infrastructure offers a broad spectrum of solutions to optimize FTTx installations. Our P350 OSP Enclosure, known for its straightforward installation and comprehensive cable management, and the FTC2 fiber wall plate, ideal for fiber interface inside the unit, exemplify adaptability and efficiency. The PR10 Media Panel is also a pivotal home connectivity hub particularly in retrofit situations, enhancing connectivity and accessibility. Service providers can use these dependable tools to ensure sustainable, cost-effective, high-speed internet access across diverse neighborhoods.
Oldcastle Infrastructure remains committed to delivering innovative tools and solutions that empower communities to succeed in the digital era. We’re here to help with FTTH projects across the US. Visit our communications solutions page to access a wealth of resources and discover our outside plant and premise connectivity product range.
Water is arguably the one asset that people take most for granted – until something goes wrong. Suddenly, it becomes expensive, scarce, and difficult to deliver. Smarter solutions make these invisible assets visible and enable city managers and water utilities to effectively tackle their critical aging infrastructure.
Water asset management: costly, complex and critical
Cities across the U.S. rely on three critical water systems to function properly:
- Stormwater networks that control runoff to manage flooding and reduce pollution in waterways
- Wastewater systems that collect, transport, and treat sewage
- Drinking water infrastructure that purifies and distributes clean water to homes, businesses, and industries
When one fails, the consequences ripple across communities.
Managing these assets has never been easy, but the task has become more complicated and costly. Climate change has intensified storms, putting additional pressures on municipalities in terms of coping with floods, mudslides and other weather-related hazards and uncertainties.
Wastewater demand fluctuates with population but becomes more expensive per capita as a community’s population and tax base drop.
As for drinking water, the losses to water main leaks and breaks are staggering. After first abstracting the water from boreholes, wells, rivers, and reservoirs, purifying it in costly filtering facilities, and sending it through a two-million-mile nationwide system of pipes, we lose about two trillion gallons a year…along with the $8 billion it costs to replace it.
As water systems become overwhelmed or break down, municipal water management leaders must wrestle with where to start as they confront aging infrastructure destined to cause significant problems in the near future.
To make matters worse, these underground assets remain invisible until failures surface – often when it’s too late.
Aging infrastructure: smarter solutions are needed
With aging infrastructure failing at an increasing rate, cities need smarter solutions.
Much of the water system in the U.S. was constructed right after World War II with an expected shelf-life of about 75 years, which means that most of the system is old beyond its time. There’s little question as to why so much of it is failing.
The ”out of sight, out of mind” nature of water loss fosters a reactive mindset among city officials and citizens alike. People in local government can agree that asset management – a comprehensive term for creating, maintaining, and updating a community’s infrastructure – is a difficult assignment. Like a homeowner postponing roof repairs, cities often delay maintenance – only to face high costs when problems become unavoidable.
The crisis of delayed maintenance for aging infrastructure is found all across the U.S., and the consequences are painful. Many communities are in a vicious downward spiral that will only get worse with ongoing failure to repair the systems.
In Jackson, MS, in 2002, a public health crisis followed the intersection of two disasters: water treatment plant infrastructure failure and river flooding. The result left 160,000 people, along with hospitals, fire stations and schools, without access to a safe supply of water. At the same time, Jackson’s water distribution system had numerous leaks and line breaks, with crews repairing five or six each day.
Stormwater itself brings miseries beyond the flooding of streets and neighborhoods. Surface water runoff is often laden with pollutants like trash, heavy metals, and bacteria that make further treatment necessary, complicated, and expensive. We see that in the Baltimore area, where aging sewer and stormwater infrastructure contributes to complications affecting a watershed that serves more than a million people.
CivilSense: making the invisible visible
Formidable obstacles stand in the way of solving the problem of aging infrastructure.
To begin with, it’s underground, hidden from easy observation and repair. When a bridge gets knocked down by a container ship or a cathedral burns out of control, the problem is readily seen and the solution obvious. But water loss is often impossible to see until the extensive damage is exposed by flooding in the streets or the water is shut off throughout entire neighborhoods.
A small puddle on the surface may be hundreds of feet from the actual source of the underground leak. What’s more, the size of the puddle tells you nothing about the size of the break. Until recently, the primary response has been with a shovel or backhoe and hours of digging.
Now, however, CivilSense™ makes sustainable water asset management efficient and effective by making the invisible visible.
Using a data-driven approach to sustainable water asset management that leverages cutting-edge technologies backed by more than 60 years of expertise and experience, city managers and water utility leaders now have a choice that pushes asset management far beyond the options that existed even as recently as last year.
New tools are available to diagnose and prioritize repair and maintenance budgets, which are only getting tighter and tighter. Real-time success stories illustrate that trusted expertise from Oldcastle Infrastructure’s team results in a near-immediate return on investment.
Investing in smarter water management today isn’t just necessary – it’s an economic imperative. With $625 billion needed over the next 20 years, solutions like CivilSense offer a way forward, delivering cost-effective, proactive asset management before crises strike.
Next
As a Thermoplastics Materials Engineer at Oldcastle, I am deeply involved in developing materials that offer protection in critical situations. My previous article highlighted how Duralite® was created to meet rigorous safety standards and flame resistance tests, all while promoting environmental sustainability. In this piece, I want to share why sustainability is personal to me—something I live every day, especially as I watch the ongoing California wildfires, which bring back vivid memories of the wildfires I’ve experienced in my home state of Oregon.
For me, sustainability is more than a goal—it’s a responsibility that extends far beyond product reliability or durability testing. It’s a mission to respond to the urgent need for a more sustainable world. And that need is more pressing than ever.
Sustainability is a term we hear frequently today. But for me—and for Oldcastle—it’s more than just a buzzword or a checkbox on a list. It’s a vital necessity that’s intricately connected to performance, and it’s woven into every step of our process: from research and development to manufacturing and distribution of products like our Duralite enclosures.
As climate-related events intensify, we feel an ever-growing sense of urgency to innovate in ways that protect our infrastructure—and the people who depend on it, including employees, customers, and communities. This urgency is what has driven us to engineer Duralite enclosures that pass rigorous Flame Spread and Enclosure Heat Protection tests. It’s also what motivates our shift from halogenated flame retardants to a safer phosphorus-based alternative that is better for the planet, its ecosystems, and its people.
Our Duralite composite body offers enhanced protection for critical infrastructure—like valves, switches, and electronics—shielding them from the devastating effects of wildfires. This, in turn, helps prevent water breaks, power outages, and ensures reliable control when it’s needed most. Each design update isn’t just an improvement—it’s a step toward a healthier, more sustainable future.
Duralite enclosures also deliver immediate safety benefits, thanks to their lighter weight and improved maneuverability, which reduce the risk of worker injury on job sites and in distribution centers. This focus on lighter weight and sustainability extends throughout Duralite’s entire life cycle, ensuring that safety and environmental impact are considered at every stage.
Products designed with sustainability in mind not only reduce harm in the short and long term, but they also contribute to a regenerative system where resources are reused rather than discarded. At Oldcastle, innovation and progress are inseparable from sustainability and safety, which is why I take my role as a Thermoplastics Materials Engineer so seriously.
To learn more about our lightweight composite enclosure, please visit our Duralite page.
As I woke up on Labor Day morning ready to make the most of the final days of summer, I looked outside and saw billowing sunlit smoke, the sign of a nearby forest fire threatening my city Portland, Oregon. It’s a stark reminder of the destructive power of wildfires and the importance of creating resilient solutions to protect our communities.
The recent California wildfires have weighed heavily on me, and at Oldcastle Infrastructure, we extend our deepest sympathies to the victims. They are a clear reminded of the Eagle Creek Fire where East winds carried the flames to the edge of Portland. It came with eye drying hot winds, ash like snow, and a total sense of helplessness as our forests burned.
As a Thermoplastics Materials Engineer at Oldcastle, I am intimately familiar with how we develop materials that protect us in critical situations. With the growing threat of wildfires, we knew we needed to create a material that was heat- and flame-resistant—the result: the Duralite® composite enclosure.
This first article explores how Duralite meets rigorous safety standards and flame resistance tests for better environmental sustainability. Featuring a thermoset composite lid and a composite plastic body, the enclosure passes the SCTE 77 Flame Spread and the Enclosure Heat Protection tests. This test involves burning the materials to measure the rate of burn and build a fire over the buried enclosure to measure the effects of heat inside.
In 2024, we transitioned from a brominated/halogenated flame retardant to a phosphorus-based flame retardant, because there’s growing evidence that halogen-free flame retardants (FRs) are safer for people and more sustainable for the environment.
Halogenated FRs are effective at preventing smoke and flames, but persist in the environment, bioaccumulate in the food chain, and disrupt endocrine systems, potentially leading to harmful health effects. Halogenated FRs break down slowly, accumulating in soil, water, and wildlife over time. As they move up the food chain, they can reach dangerous concentrations in predators. Studies suggest potential developmental, reproductive, and immune system impacts. When disposed of improperly, halogenated FRs can leach toxic chemicals into the environment, contributing to long-term pollution.
At Oldcastle, we strive to make products that meet the highest safety standards and contribute to environmental sustainability. While our Duralite composite body was designed to meet the load-bearing specifications of concrete alternatives, we’ve taken the extra step of using recycled plastic as the primary material. Blending recycled plastic with engineered additives achieves the required strength while reducing our environmental impact.
Our first successful Duralite bodies were made with some of the dirtiest recycled plastics— water bottle caps and closures. We rigorously test all incoming recycled materials to ensure our products meet or exceed performance standards. Compared to new plastic, recycled plastic emits 50% less greenhouse gas (GHG) per weight.
A Duralite enclosure is also significantly lighter than concrete alternatives and produces far fewer GHG emissions. We take a circular sustainability approach. When the enclosure reaches the end of its life, it can be ground up to create new products. We recycle our own Duralite process scrap to produce fresh enclosures. Duralite is not just a high-performance solution; it’s also the most sustainable choice available.
To learn more about our lightweight composite enclosure, please visit our Duralite page.
On January 23, 2025, the U.S. House of Representatives passed the Fix Our Forests Act, a bipartisan bill designed to reduce the risk of devastating wildfires. This legislation will help electric cooperatives by expediting federal approval for grid hardening and allowing the removal of hazardous vegetation that could fuel fires. Both measures aim to prevent future wildfire disasters.
In recent years, the U.S. has faced catastrophic wildfires causing billions in damages and displacing thousands of people. Many of these fires have been linked to electrical equipment failures or power lines sparking in areas overrun with vegetation. For instance, the 2018 Camp Fire in California, sparked by electrical transmission lines, tragically claimed 85 lives and destroyed the town of Paradise. Similarly, the 2023 Maui wildfires and the 2025 Palisades wildfires highlighted how failures in electrical systems and vegetation management can result in significant loss.
The Fix Our Forests Act aims to streamline the process for electric cooperatives to obtain federal permits to modernize their systems and enhance their resistance to wildfires. Currently, cooperatives can only remove vegetation within 10 feet of power lines and rights of way. This bill expands that limit to 150 feet, allowing them to proactively clear hazardous trees that could fall and spark fires. The bill now awaits approval from the Senate, which could be a critical step toward preventing future wildfires.
As wildfire activity and extreme heat waves become more frequent, electric utilities must prioritize fire resistance when selecting underground enclosures, especially in high-risk areas. The ANSI/SCTE 77 guidelines include flammability testing (Section 6.5) and internal equipment protection (Section 6.6) to assess how enclosures withstand fire exposure. Flammability tests (ASTM D635) measure how easily a product ignites and burns, while internal protection testing (USDA RUS 7 CFR 1755.910) ensures underground equipment remains functional in the event of a fire above the enclosure.
Oldcastle’s Duralite® enclosures exceed all industry standards for fire resistance and internal equipment protection. They maintain safe internal temperatures even when exposed to brushfire conditions exceeding 1,000°F. Duralite® has undergone third-party testing to meet GR-902-CORE, SCTE 77 2023, and USDA RUS 1755F 910 standards. By choosing fire-resistant enclosures, utilities can ensure long-term protection of underground assets, minimizing the risk of wildfire-related damage.
Bill Overview:
- Introduced by Rep. Bruce Westerman (R-AR) and Rep. Scott Peters (D-CA)
- Passed the House with bipartisan support (279-141)
- A previous version of the bill passed last September, but the Senate adjourned before acting. The current version now awaits Senate approval, which could be key in preventing future wildfire catastrophes.
As electric vehicles (EVs) become increasingly popular, the demand for a robust charging infrastructure is also growing. Traditional methods of building charging stations, especially in established sites, can be slow, costly, and disruptive. This creates delays in expanding the necessary charging networks. Platform-based designs for EV charging—like the DC-America platforms offered in partnership with Oldcastle Infrastructure—provide an innovative, faster, cost-effective, and scalable solution to meet the rising demand for charging stations.
Cost Efficiency and Faster Deployment
Platform-based designs bring significant savings in both cost and time. These prefabricated, standardized platforms eliminate the high costs typically associated with custom-built stations. They are flexible enough to fit various locations while meeting specific customer needs, offering a combination of affordability and adaptability. Standardizing platform sizes and manufacturing processes reduces material waste and lowers labor costs. This approach can reduce construction costs by up to 15% and cut installation time by as much as 50%, accelerating deployment and ensuring charging stations are installed where they’re most needed.
Simplified Engineering and Installation
Platform-based designs also streamline engineering and installation processes. Constructed with high-quality U.S.-made steel and featuring simplified electrical systems, these platforms reduce complexity. Most Electric Vehicle Supply Equipment (EVSE) uses similar designs, making wiring integration easier. The platforms include an enclosed raceway for electrical and communication cables and a single-point power connection, enhancing installation efficiency. This not only cuts labor costs but also speeds up the process, enabling stations to start operating sooner.
Reduced Site Work and Rapid Deployment
Traditional construction often requires extensive site preparation, including removing asphalt, pouring concrete, and laying conduit. Platform-based designs require minimal site preparation, significantly reducing installation time and costs. Additionally, they reduce material waste and environmental impact. Since these platforms are pre-manufactured and pre-commissioned in climate-controlled facilities, weather conditions are less likely to delay installation, making the process more reliable.
One of the key benefits of platform-based depots is their rapid deployment. Delivered as fully assembled units, these platforms only need to be offloaded, set in place, and anchored. This process can be completed within hours, with minimal disruption to the surrounding area. The quick setup accelerates return on investment (ROI) and ensures that charging stations are operational almost immediately.
Scalability and Future-Proofing
In addition to being cost-effective and fast, platform-based depots are scalable and adaptable to future needs. These systems can easily be relocated, expanded, or upgraded as demand increases or as new technologies emerge. Operators can add new platforms to increase the number of chargers or upgrade existing ones to accommodate future advancements in charging technology. The modular design also allows for easy equipment replacement without requiring extensive demolition, ensuring the long-term sustainability of the infrastructure.
Moreover, platform-based depots offer ample customization options, including features such as lighting, cameras, and photovoltaic canopies, which enhance the user experience and further reduce construction time and costs. This flexibility ensures that charging stations remain efficient, functional, and adaptable for years to come.
A Critical Role in EV Infrastructure Expansion
As the EV market grows, platform-based depots will play a crucial role in expanding the charging infrastructure. These systems provide a cost-effective, efficient, and scalable solution that accelerates deployment while minimizing disruption to the surrounding environment. Innovations like the DC-America platform, in partnership with Oldcastle Infrastructure, are helping deliver faster ROI, shorter installation times, and long-term sustainability.
Platform-based EV charging depots are helping create a more accessible and efficient transportation network, ensuring that the growing needs of the electric vehicle market are met with speed, affordability, and future-proof flexibility.
We’re here to help with your EV charging projects across the US. Visit EV Charging Infrastructure Solutions Center to access a wealth of resources and discover our extensive and adaptable product range.
The importance of stormwater maintenance
When it comes to stormwater treatment, much emphasis is given to performance. Testing verification and protocols such as New Jersey’s NJCAT and Washington’s TAPE assess the pollutant removal rates of stormwater separators and filters, and they provide valuable like-for-like comparisons that assist engineers in specifying the most effective treatment solution for the site.
However, the stated performance of any system is contingent on the operating condition of that system.
The Prussian general Helmuth von Moltke once suggested that “no plan survives first contact with the enemy”, and I think a similar principle may be applied here: no unmaintained stormwater treatment system survives extended contact with the real world.
What do I mean by that? Simply put, a typical surface water treatment system is designed to capture and remove pollutant materials from stormwater. This ranges from trash and gross solids to nutrients, heavy metals and hydrocarbons, all while having defined storage capacity for these materials. If left unattended, it will eventually fill and its capacity to store pollutants will be lost. Its performance will drop to zero, and it could eventually create a flood risk by preventing water from flowing at all.
All stormwater systems need to be maintained—green or grey, natural or engineered—and ironically, the better the system performs, the faster it will fill up.
So while performance is the fundamental characteristic of any stormwater treatment system, without regular maintenance, that performance eventually means nothing.
Maintenance: a shared responsibility
Responsibility for the operation and maintenance of a surface water treatment system ultimately lies with the site owner, but they are often unaware that they even own such a system.
The consultants, design engineers and contractors who deliver the project are custodians of the site before and during development, and as such they share a duty to ensure that the site that they pass on meets all necessary regulations—now and in the future.
Engineers in particular are uniquely placed to position a site for long-term environmental compliance. The lifetime of a stormwater treatment system is measured in decades, so the selection of that system will determine how effectively stormwater is managed on the site for many years.
The engineer has a delicate task, having to balance client expectations against regulatory compliance and cost effectiveness against performance. It would be easy to sacrifice long-term performance for short-term benefit. Fortunately, however, modern systems such as the Hydro-Shield™ Advance hydrodynamic separator are increasingly engineered to operate in a sweet spot that provides affordable high-performance treatment with quick, easy maintenance.
Contractors also bear responsibility for handing over a site that is optimized for effective long-term stormwater management, and they can benefit from doing so. More and more construction companies are recognizing that sustainable development and environmental stewardship are valued by shareholders, employees and the communities in which they live and work. Demonstrating that procurement decisions have been made with sustainability in mind has both environmental and commercial benefits.
How to maximize stormwater treatment operating efficiency
Maintenance is often thought of as a post-install responsibility, but engineers and project owners should keep operating efficiency and system lifetimes in mind from the very start.
Good project operation and efficient maintenance begin with design and continue through installation, and these aspects are influenced by decisions made and actions taken early on in the project.
Adopting the following three principles at early and intermediate stages of the project will help to maximize the operating efficiency of the stormwater treatment systems for the lifetime of the site development.
Design stormwater with maintenance in mind
Stormwater regulations persist for the lifetime of the site, so engineers should optimize the design of the site so that the site owner is enabled and empowered to remain compliant with regulations and protect the local environment from surface water pollution for the lifetime of the site development.
Clearly engineers approach the design process with regulations and performance at front of mind, but optimizing for lifetime performance means going beyond that. Not only should the stormwater management systems themselves be quick, easy and safe to maintain, but the site overall should accommodate maintenance in a way that does not impinge on that.
Site features and components should improve—or at the very least not hinder—access for ongoing maintenance. Vehicle access should be safe and secure, for example, and wherever possible, maintenance access points should be sited in such a way that maintenance vehicles do not block or impede road users or pedestrians.
Safety should also be paramount. Maintenance work can be risky, so particular attention should be paid to systems and features that remove, minimize or mitigate risk to maintenance workers and the public. Access to stormwater systems should be quick and simple, and engineers should prioritize systems that limit the time that maintenance personnel spend in confined spaces or operating machinery. Ease and speed of maintenance are key.
Develop an effective maintenance plan
Site plans governing the operation and maintenance of surface water management systems on site are an essential tool for the owner, engineer and contractor alike—and in fact may be required by local planning regulations.
As part of the site development process, the engineer and contractor should develop a maintenance plan or operation and maintenance (O&M) manual. This document will provide site owners with all the information that they need in order to monitor, clean, repair or replace any parts of their stormwater management system necessary to remain compliant.
Indeed, the EPA recommends that any stormwater maintenance plan clearly defines who is responsible for maintenance, what maintenance activities are required and how frequently they are carried out, what level of funding is required, and so on. Individual states may also provide their own recommendations or templates based on local requirements.
The plan should provide a site owner with all necessary information required to inspect, operate and maintain stormwater management infrastructure. This should include maintenance requirements for component parts, schedules for inspections and site visits and instructions on how to report and record repairs.
The plan can also help the owner budget for the required maintenance, to prevent any financial surprises down the line. Most manufactured treatment devices have O&M manuals that can form the basis for such a plan.
This plan should form part of a site handover, giving owners a clear step-by-step guide to maximizing system performance and operating efficiency for the duration of its lifetime.
Use handover as an opportunity to add value
Stormwater treatment systems are often one of the first components of a development to be installed, sometimes a number of years before completion of the overall project. Typically they are underground, and the owner is likely to be distanced from the project due to there being a substantial number of other parties involved. When it comes time to take ownership of the site they are likely to have a range of other competing priorities.
As the subject-matter experts, prior to and during handover, consultants and designers should take the opportunity to underline to the owner the importance of carrying out the correct maintenance of the system. Proper maintenance supports both the expected performance and lifespan of the system.
Site owners are likely not to be experts in stormwater management, so engineers can provide value by educating the owner on the need for maintenance. They can recommend that maintenance be overseen or carried out by a party with knowledge or expertise of stormwater management.
They may also advise that the equipment manufacturer provide expert inspections for an initial period while the site owner manages a newly completed project. We recommend scheduling regular inspections on stormwater treatment systems for a minimum of two years after installation.
Finally, it is common for systems to be “lost” after construction, and for owners to be completely unaware of them. Owners and regulatory inspectors rarely own the original drawings and plans. Engineers can benefit all involved by pushing for all installed systems to be captured in a geographic information system (GIS) to eliminate this knowledge gap and aid in regulatory compliance.
Conclusion
Undertaking the correct maintenance program is the most cost-effective long-term approach for the site owner. Maintaining the stormwater treatment systems installed on their site helps the owner to avoid costly fines, bad publicity and legal issues resulting from non-compliance with regulations.
By outlining these risks and helping the owner to plan to mitigate them, engineers provide additional value to clients, partners, and the public and position themselves to win further business.
Next
In my previous article, I delved on the differences in quality and control, speed of installation, labor resources and risk concerns between pre-cast and cast-in-place (CIP) construction methods. This article focuses on the vast difference between price and total cost of ownership (TCO) and why it is an important consideration when planning EV charging projects.
While precast solutions may come with a higher upfront cost, it often results in significant long-term savings. For example, while the material and installation cost for a precast underground structure might higher, the TCO of CIP may start much lower but increase when accounting for the additional time and labor required. The extra days of work required for CIP—due to pouring, curing, and finishing—adds not only labor costs but also general conditions costs (supervision, insurance, jobsite overhead, etc.).
We estimate an average of about 20 percent savings in a double pad installation:
Cost Comparison of Precast to Cast-in-Place EV Charging Double Pad Installation
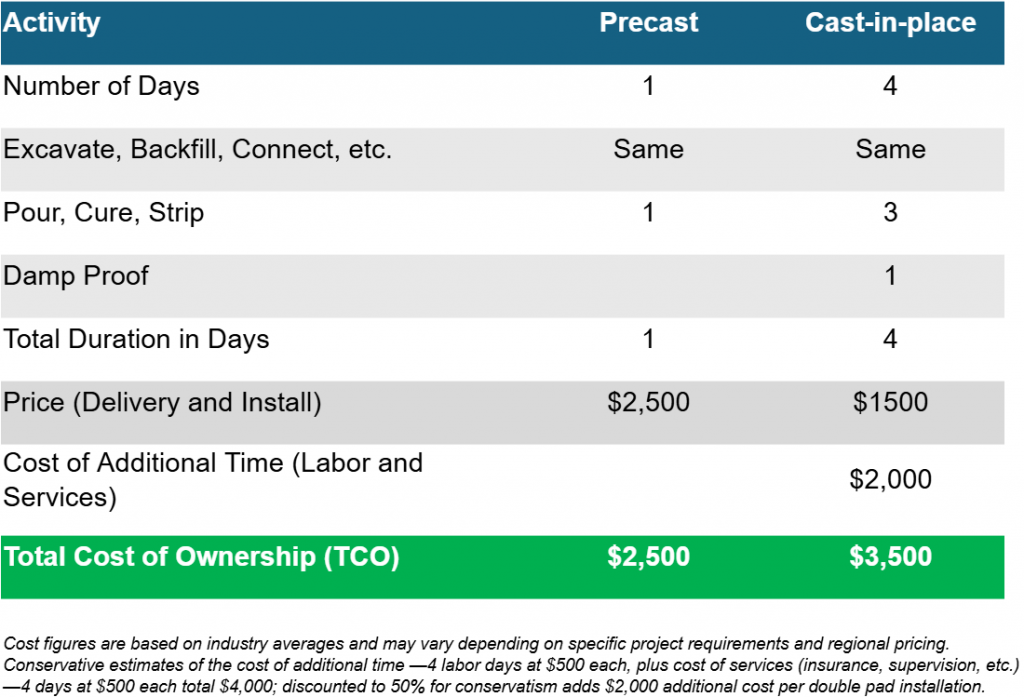
In this example, even if CIP seems cheaper initially, the TCO ends up being higher due to extended project timelines and the added risk of delays or errors. Precast product’s faster installation helps save on additional time costs, and for contractors, every saved day equates to increased profitability.
Real-World Example: Cost Breakdown
Consider the above example of installing a double pad underground structure for an EV charging station. A precast unit would cost on average $1,500, with an additional $1,000 for crane services. Installation is completed in one day, including backfill, with no curing time required. On the other hand, CIP for the same structure, requiring labor for multiple pours, curing, and damp proofing, totals $1,500 for the materials alone, but the TCO increases once you factor in the extra time and labor.
Saving this extra time and labor means additional profit for the contractor and faster monetization for the site owner. When considering general condition costs, this savings could rise further. Precast offers a substantial reduction in the total cost compared to CIP, with potential higher savings depending on weather
Precast is the Better Choice
While CIP may offer advantages in certain cases—such as highly customized designs or challenging site conditions—precast solutions generally provides a better value for EV charging installations. The time savings, reduced labor, consistent quality, and lower TCO make precast the more efficient, cost-effective solution in most cases. When choosing between these two methods, contractors and specifiers should focus on the total cost of ownership rather than just the upfront price, recognizing that precast offers long-term savings that far outweigh its initial cost.
We’re here to help with your EV charging projects across the US. Visit EV Charging Infrastructure Solutions Center to access a wealth of resources and discover our extensive and adaptable product range.
When planning the installation of electric vehicle (EV) charging stations, selecting between precast solutions and cast-in-place (CIP) is a crucial decision that influences both immediate expenses and long-term value. This choice requires a comprehensive understanding of the Total Cost of Ownership (TCO), encompassing four key components: quality, installation, delivery, and upfront cost.
This article focuses on differences in quality and control, speed of installation, and labor and risk considerations. The next article in this series will offer a comparison between price and TCO.
Understanding Total Cost of Ownership (TCO)
TCO extends beyond the initial material costs to include all expenses over the project’s lifespan. It comprises:
- Quality: The durability and reliability of the concrete, impacting long-term performance.
- Installation: The efficiency of the installation process, including labor requirements and construction scheduling.
- Delivery: The time taken to receive materials on-site and complete the installation.
- Upfront Cost: The cost of materials and installation.
While precast solutions may have a higher upfront cost compared to CIP, the other TCO components often make it the more advantageous choice when evaluating long-term costs.
Quality and Control
Precast offer superior quality control during manufacturing. Produced in a controlled factory environment, precast products ensure consistent strength, durability, and dimensional accuracy. This process eliminates the variability and potential issues associated with CIP, where factors such as weather conditions, on-site mixing, and curing times can affect the final product’s quality.
For EV charging installations, where durability and reliability are paramount, precast solutions ensure the structure will withstand wear and tear over time. In contrast, CIP concrete, poured and cured on-site, is more susceptible to unpredictable elements, leading to a higher risk of defects or the need for repairs down the line.
Speed of Installation and Time Savings
Precast solutions offer significant time savings over CIP. Precast components are manufactured off-site and delivered ready to install, allowing for a quicker installation process without the need for curing or formwork setup. For an EV charging station, which may require a quick turnaround, the reduced time spent on-site can be a major advantage, enabling more installations per day to shorten project timelines.
In a typical precast installation, delivery and installation can be completed in just one day, while CIP may take up to seven days due to the time required for pouring, curing, and stripping the forms. The time savings associated with precast not only accelerate the project timeline but also reduce the risk of delays and associated costs, such as extended labor and equipment rentals.
Reduced Labor and Risk
Precast solutions reduce the amount of labor needed on-site, as the components are pre-made and simply require lifting and positioning. This reduces the complexity of the construction process, minimizing the potential for errors and delays. One typical error encountered is concrete poured on incorrect rough-in of conduits and anchors.
CIP, however, requires more on-site labor, including formwork setup, pouring, finishing, and curing. Additionally, the construction schedule is more unpredictable, as it is subject to weather and other environmental factors, any unexpected rain fall could delay installation for the day or affect the curing of any CIP concrete poured prior to the rain fall. For EV charging stations, where downtime can disrupt service, using precast products ensures faster deployment, reducing potential loss of business.
We’re here to help with your EV charging projects across the US. Visit EV Charging Infrastructure Solutions Center to access a wealth of resources and discover our extensive and adaptable product range.
As renewable energy generation expands, the need for a more flexible, resilient, and efficient U.S. energy grid has become urgent. The shift toward cleaner energy sources like solar and wind is reshaping the grid, creating both challenges and opportunities.
While the first Trump administration focused on deregulation and energy independence through fossil fuels, it also recognized the importance of renewables like wind and solar, supporting their growth through incentives such as the Production Tax Credit (PTC) and Investment Tax Credit (ITC). Continued support for these sectors will be essential to ensure that the grid can accommodate the increasing influx of clean energy.
Challenges of Geographic Mismatch in Renewable Energy Generation
Renewables like solar and wind are often generated in remote areas far from population centers, creating challenges in transporting energy efficiently over long distances. During the first Trump administration, infrastructure investments primarily targeted traditional energy sectors, but the transition to a cleaner energy future necessitates substantial upgrades to grid infrastructure.
A modernized grid, incorporating technologies like smart grids, will be vital for managing the intermittent nature of renewable energy and ensuring that renewable electricity can be delivered reliably to consumers. Innovations like real-time monitoring, predictive analytics, and automated responses will enhance grid efficiency and resilience.
The Role of Energy Storage in Grid Modernization
Energy storage is key to overcoming the challenge of renewable energy intermittency. The first Trump administration had mixed policies regarding energy storage, but the demand for advanced storage solutions has grown alongside the expansion of renewables.
Energy storage systems allow excess energy generated during peak renewable production to be stored for later use when production is low. Battery storage, along with other technologies, helps smooth out fluctuations in supply, making the grid more reliable.
As storage costs continue to decline, large-scale storage projects are increasingly being implemented across the U.S. This integration will be essential for ensuring that clean energy can meet demand at all times.
The Growing Demand for Electricity: EVs and Data Centers
In addition to traditional energy demands, the growing need for electricity from electric vehicles (EVs) and data centers presents new challenges for the grid. EVs are expected to make up a large portion of transportation in the coming decades and will require substantial amounts of energy for charging. Similarly, the rise of data centers—critical infrastructure for the digital economy—will further strain the grid.
The increasing importance of renewable energy for these sectors underscores the need for grid adaptations that integrate sustainable power sources to meet future demands.
State-Level Renewable Energy Goals and Grid Challenges
Many states across the U.S. have set ambitious renewable energy targets, with some aiming for 100% renewable energy portfolios. As these state-level goals advance, grid operators face the challenge of managing the growing influx of renewable energy while maintaining grid stability and reliability.
Ensuring that the grid can handle both the quantity and variability of renewable energy will require significant infrastructure investment, technological upgrades, and collaboration between utilities, regulators, and developers. Successfully integrating renewables without compromising grid performance will be a critical priority as state-level goals progress.
Preparing the U.S. Grid for a Sustainable Future
The future of the U.S. energy grid will require extensive collaboration and ongoing technological innovation. As renewable energy becomes a more significant part of the U.S. energy mix, the grid must be modernized to support these sources. This includes the integration of solar, wind, and storage systems while accommodating new demands like electric vehicles and data centers.
To achieve this, continued investments in grid infrastructure, energy storage solutions, and smart grid technologies will be essential. With the right policies and investments, the U.S. can build a grid capable of supporting a clean, secure, and sustainable energy future that meets the needs of both current and future electricity consumers.
Oldcastle Infrastructure is your partner in renewable energy infrastructure projects. Explore our energy solutions designed to power projects toward a sustainable, electric-powered future at: Manufacturer of Electric, Oil, & Gas Utility Infrastructure Precast & Enclosure Solutions | Oldcastle Infrastructure
Utilities are central to the U.S. renewable energy transition, with a growing emphasis on clean energy driven by favorable economic conditions, supportive policies, and increasing demand for sustainable energy.
Meeting the Growing Demand for Clean Energy
The transition to renewable energy is heavily driven by growing consumer demand. As individuals and businesses seek to reduce their carbon footprints, utilities are pressured to offer cleaner energy options. This consumer-driven demand pushes utilities to accelerate their renewable energy investments, which helps them meet renewable portfolio standards (RPS) and clean energy standards (CES) set by individual states and at the federal level.
Additionally, utilities are under increasing pressure from investors and stakeholders to shift their energy mix toward renewables. The growing emphasis on environmental, social, and governance (ESG) factors in investment decisions is influencing utilities to diversify their portfolios away from fossil fuels and toward cleaner, more sustainable energy sources. These pressures, combined with a desire to stay competitive in a rapidly evolving energy market, are driving utilities to expand their renewable energy offerings.
Utility Involvement in Wind and Solar Projects
Utilities are essential in the transition to renewable energy by ensuring the integration of solar and wind power into the electrical grid. They do this through Power Purchase Agreements (PPAs), direct project ownership, grid integration, energy storage, and collaboration on siting and permitting of renewable projects. By partnering with independent power producers (IPPs), utilities can leverage expertise and funding to assist in the development of these projects. For example, the Midwest has seen a surge in wind power investments in Kansas, Oklahoma, and Colorado, which benefit from some of the best wind speeds in the country. Similarly, solar energy investments are flourishing in states like California, Texas, and Florida, which have become leaders in the adoption of solar power.
Utility investment in large-scale solar and wind energy projects is also fueled by tax incentives, the U.S. government’s shifting policies toward cleaner energy, and some cost reductions in renewable technologies. Tax credits for these industries—such as the Investment Tax Credit (ITC) for solar and the Production Tax Credit (PTC) for wind—remain intact, encouraging significant investments in renewable infrastructure.
The Road Ahead for U.S. Utilities and Renewable Energy
As utilities continue to invest in renewable energy, they are not only contributing to the fight against climate change but also position themselves for the future. The shift from fossil fuels to renewables is a critical component of the nation’s energy strategy, with utilities playing a pivotal role in expanding solar and wind capacity.
With the continued evolution of energy policy, technological advancements, and growing consumer demand for cleaner energy, utilities will play a vital role in shaping the future of renewable energy in the United States.
Oldcastle Infrastructure is your partner in renewable energy infrastructure projects. Explore our utility distribution solutions—including our Highline and Nordic brands—designed to power projects toward a sustainable, electric-powered future at: Electric Utility Infrastructure Precast & Enclosure Products | Oldcastle Infrastructure
BABA Certified Infrastructure for Smart Cities
As cities become smarter, reliable communication infrastructure is necessary to support evolving social and economic needs. BABA certification supports that transition.
As cities evolve into smart urban centers designed to support work, play, and living, the need for reliable communication infrastructure becomes more critical.
Federal programs supporting communication service providers enable high-speed connectivity and the technologies that drive smart cities forward.
One cornerstone of these federal initiatives is the Build America, Buy America (BABA) certification, which ensures that materials used in broadband deployments are domestically sourced and meet rigorous federal standards.
This certification plays a key role in ensuring that the infrastructure supporting smart cities is both high-quality and reliable, giving developers, planners, and policymakers confidence in the systems they implement.
The Importance of BABA in Smart City Infrastructure
Smart cities rely on integrated systems to enable technologies like the Internet of Things (IoT), smart grids, and other next-gen solutions. BABA-certified products are crucial to building these systems.
For example, Oldcastle Infrastructure’s Duralite® lightweight enclosures, engineered for tier 15 and tier 22 loads, are indispensable in forming the infrastructure backbone of these cities, ensuring the correct connections are made to enable data to flow securely.
In addition, Oldcastle’s Primex product line offers fiber-to-the-home solutions, including fiber interface (NID) enclosures and premise distribution components, both used to design and enable high-speed internet service deployments.
Our BABA-certified products meet the rigorous standards of the Broadband Equity, Access, and Deployment (BEAD) Program, which directs $42.45 billion toward enhancing high-speed internet access in underserved areas.
We expect these standards to be part of other future funding programs as this approach not only promotes American manufacturing but also guarantees that the infrastructure built for smart cities is robust, sustainable, and reliable.
Streamlining BABA Compliance
BABA compliance strengthens the integrity of the BEAD Program by ensuring that only domestically produced equipment is used, reinforcing the commitment to American manufacturing and securing eligibility for federally funded projects. Compliance also benefits manufacturers by enhancing their reputation and increasing their competitiveness in the market.
The Department of Commerce plays a critical role in this process by maintaining a BABA Self-Certification list. This tool allows manufacturers to demonstrate their products meet domestic manufacturing standards, providing transparency to service providers and contractors.
This makes it easier for stakeholders to select certified products and ensures that companies like Oldcastle remain trusted partners for federally funded infrastructure projects.
Commitment to American Manufacturing
Oldcastle Infrastructure proudly supports U.S. manufacturing through its extensive network of facilities that serve the communications, energy, and water infrastructure markets.
Next
The US stormwater sector is highly regulated, with stormwater testing protocols such as NJCAT and TAPE setting a high standard for pollutant removal performance. However, engineers will benefit their clients and their communities by looking beyond the test.
The stormwater sector in the US is highly regulated, and these regulations are what help to ensure that our surface water is appropriately treated to remove damaging pollutants before they are able to reach the environment.
In implementing these regulations, some states have developed or adopted testing protocols in order to ensure that manufactured treatment devices (MTDs) and other stormwater best management practices (BMPs) meet performance standards. Systems and technologies that verifiably meet these standards are certified or approved and thereby made available to engineers.
Prominent testing frameworks include New Jersey’s NJCAT and Washington’s TAPE programs, with many jurisdictions around the country also accepting certifications from these programs.
The great strength of these testing protocols is that they level the playing field, create consistency and provide engineers with a list of options that meet performance standards.
However, in addition to that strength there is also an opportunity.
Maximum treatment flow rate
In order to create consistency and a level playing field, the tests typically require systems to demonstrate that they remove a certain percentage of a particular pollutant; all systems that pass the test achieve that percentage removal rate by definition, so the only differentiation between them that engineers can make is in the maximum treatment flow rate (MTFR) of the system.
As an example, one system might remove 50% of total suspended solids (TSS) at an MTFR of 5 cfs, while another system might remove 50% at 6 cfs.
This can be helpful, but what is not always well understood is that the MTFR and its associated removal rate is not a simple number; rather it is a weighted aggregate of different removal rates at a range of different flows, designed to provide an overall average removal rate over the course of a typical year of annual precipitation.
For example, a system might remove 70% of TSS at 10% of MTFR and remove 30% of TSS at 150% of MTFR, with a range of other removal rates for the other different flow rates in between. Overall, with different weightings given to the different flow rates, that might equate to an aggregate removal rate of 52% at the given MTFR.
In this way, stormwater testing accounts for seasonal variations in rainfall, ensuring that the system provides greater protection from the more frequent smaller storms that generate the bulk of the pollutant load, while also providing protection from the less frequent but more intense storms. In other words, the test attempts to simulate the flows that a system might encounter in the real world.
Stormwater testing and treatment performance in the real world
While stormwater testing protocols such as these are a good approximation of real-world conditions, they are necessarily an abstraction, however, and a range of confounding environmental factors can affect performance, including temperature, influent particle size and the hydraulic characteristics of the surrounding network.
Under these conditions stormwater treatment systems don’t always operate predictably. For example, stormwater samples tested at our Portland, ME hydraulics lab has indicated that for the Up-Flo® Filter, higher pollutant loading rates correlate with higher percent removals: as the concentration of TSS increases, so does the percent removal.
Our new Hydro-Shield™ Advance hydrodynamic separator has been recently certified by the New Jersey Corporation for Advanced Technology and achieved the protocol’s 50% TSS removal rate with the highest flow rate of any system under its newest test protocol, and while I’m delighted that we’ve developed the leading stormwater separator on the market, I know that the system’s truest test will be under the conditions that it will face in the field.
And of course we should keep in mind the non-performance aspects of systems such as these. For example, smaller footprints can mean that installation is easier, cheaper and—most importantly—safer for contractors, while improved maintenance access can help to ensure that systems continue to perform as designed long after they’ve been installed. After all, test results doesn’t mean much if a system has been left to clog up.
The opportunity lies beyond the test
Therein lies the opportunity. The test results indicate which companies have the technical expertise to design a system that performs, but this should be the start of the conversation rather than the end.
All stormwater separators remove TSS, but which are optimized for maintenance? Which are quick and easy to install? Which are made sustainably? Looking beyond the system itself, which companies provide reliable technical information, design support and tools? Finally, which companies provide reasonable lead time delivery and installation support after the sale is made?
All these things must be considered for the design engineer to make the right choice for the project owner.
Stormwater testing protocols such as NJCAT and TAPE are necessary and valuable, and they provide the consistency and minimum performance levels that we need to protect our environment from stormwater pollution. However, if engineers focus overly on the results in the lab then they run the risk of underemphasizing the way a system will perform where it really matters: in the ground.
I would urge specifying engineers to use approvals, verifications and certifications as an initial menu of options, but then to partner with providers that go beyond the test to deliver the real-world performance and practical considerations that ultimately improve design, installation and long-term stormwater management.
Next
In today’s connected world, broadband access is essential. A 2021 study by Microsoft revealed that approximately 120.4 million Americans use broadband internet, but millions of people still face barriers to reliable service. According to Broadband Now, over 42 million Americans lack adequate broadband, further deepening the digital divide and limiting access to critical opportunities for education, business, and personal growth.
A promising solution to this problem lies in Fiber to the Home (FTTH) technology, which delivers fast and reliable internet by running fiber optic cables directly to homes. This method allows for quicker, more stable connections that meet the growing demands of modern internet use.
Electric Utilities Stepping into the Broadband Arena
While electric utilities have traditionally been responsible for delivering power, many are now stepping into the broadband space. Recognizing that access to high-speed internet is just as crucial as reliable electricity, utilities are increasingly using their existing infrastructure—such as power lines and rights-of-way—to support broadband deployment, especially in rural and underserved areas.
This shift is particularly significant in rural communities where traditional broadband providers may not be willing or able to invest. By leveraging their existing networks, utilities are uniquely positioned to bring internet access to areas that have long been left behind.
Cooperatives and Municipal Utilities at the Forefront
Cooperatives and municipal utilities are playing a central role in broadband expansion, particularly in rural regions. These local entities, which have a deep understanding of their communities’ needs, are ideal partners for broadband initiatives. For example, in Alabama, eight rural electric cooperatives have joined forces to form a single entity focused on broadband expansion. Their collaborative efforts have already led to job creation and an estimated $500 million in economic impact.
The National Rural Electric Cooperative Association (NRECA) has provided critical support to these utilities, helping them navigate the complexities of FTTH deployment. By tapping into these resources, cooperatives are overcoming the barriers to broadband access and driving economic growth in their regions.
Public Utilities Accelerating Broadband Access
Public utilities, too, are key players in expanding broadband. Many public power providers are taking steps to enhance their broadband offerings by partnering with local stakeholders and investing in infrastructure. With their existing infrastructure and local connections, public utilities are well-positioned to extend broadband access to underserved communities.
A New Role for Utilities in the Digital Age
The growing involvement of electric utilities in broadband expansion marks a major shift in the utility landscape. No longer focused solely on delivering electricity, utilities are becoming key players in the effort to provide reliable internet access to all Americans. By utilizing their existing infrastructure and forming strategic partnerships, utilities are helping to ensure that high-speed internet reaches even the most remote areas.
As utilities continue to embrace broadband deployment, they are playing a critical role in creating a more connected, digitally inclusive future. By working together with local communities, these utilities are bridging the digital divide and powering a new era of economic opportunity.
The involvement of electric utilities in FTTH expansion represents a promising solution to the nation’s broadband challenges and Oldcastle Infrastructure can help electric utilities build the underground network and connect it to the premise. Check out our communications solutions at: Communications Solutions | Oldcastle Infrastructure